The Scientific Research Behind Porosity: A Comprehensive Guide for Welders and Fabricators
Recognizing the complex devices behind porosity in welding is vital for welders and fabricators pursuing flawless craftsmanship. As metalworkers look into the midsts of this sensation, they reveal a world regulated by numerous aspects that influence the formation of these minuscule gaps within welds. From the structure of the base materials to the intricacies of the welding procedure itself, a plethora of variables conspire to either intensify or alleviate the existence of porosity. In this thorough overview, we will untangle the scientific research behind porosity, discovering its results on weld top quality and unveiling advanced strategies for its control. Join us on this trip via the microcosm of welding imperfections, where accuracy meets understanding in the pursuit of perfect welds.
Comprehending Porosity in Welding
FIRST SENTENCE:
Examination of porosity in welding exposes critical insights into the honesty and top quality of the weld joint. Porosity, defined by the visibility of tooth cavities or spaces within the weld metal, is a typical concern in welding procedures. These gaps, if not appropriately addressed, can endanger the structural honesty and mechanical residential properties of the weld, leading to possible failings in the completed item.
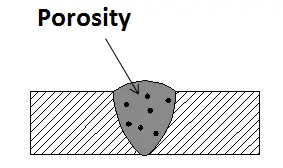
To discover and evaluate porosity, non-destructive testing techniques such as ultrasonic screening or X-ray examination are usually utilized. These strategies enable the recognition of interior problems without compromising the integrity of the weld. By examining the size, shape, and distribution of porosity within a weld, welders can make informed decisions to improve their welding procedures and achieve sounder weld joints.
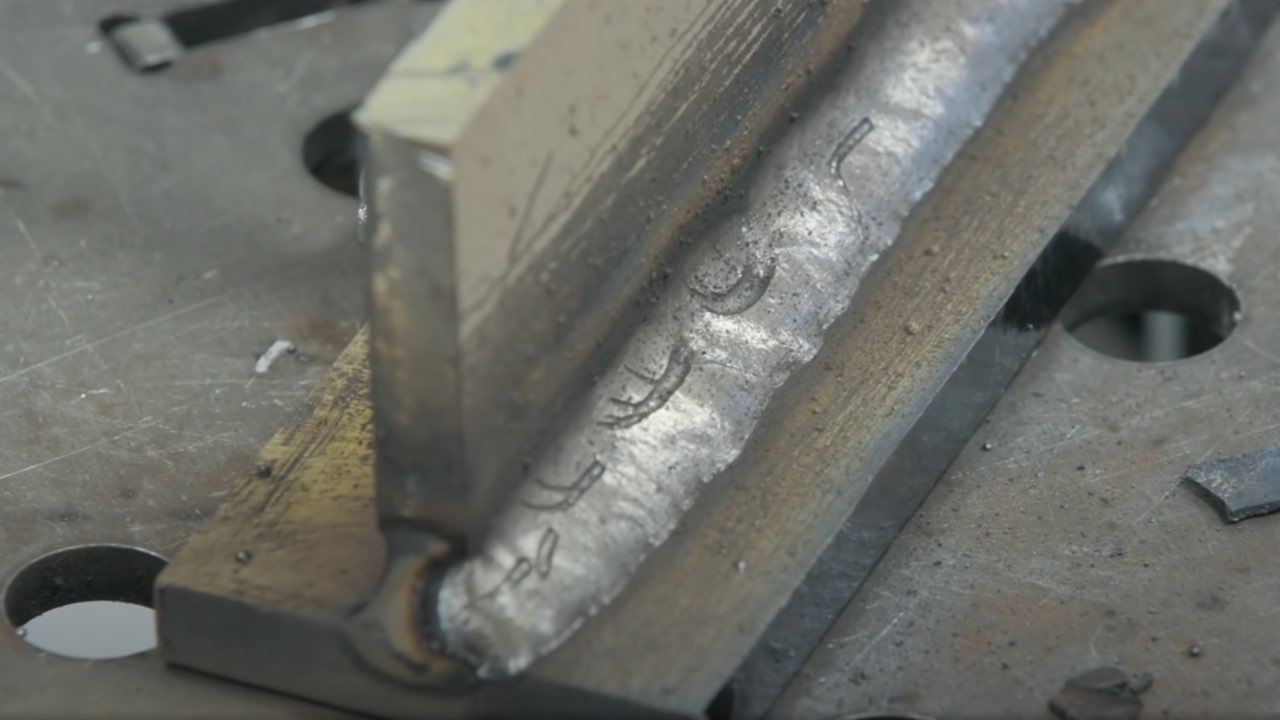
Factors Affecting Porosity Formation
The occurrence of porosity in welding is influenced by a myriad of aspects, ranging from gas shielding effectiveness to the intricacies of welding specification settings. Welding parameters, including voltage, existing, travel speed, and electrode kind, additionally impact porosity formation. The welding method used, such as gas steel arc welding (GMAW) or shielded steel arc welding (SMAW), can affect porosity development due to variants in heat distribution and gas coverage - What is Porosity.
Impacts of Porosity on Weld Quality
Porosity formation significantly jeopardizes the architectural integrity and mechanical residential or commercial properties of bonded joints. When porosity is existing in a weld, it creates voids or tooth cavities within the product, minimizing the overall strength of the joint. These voids work as stress concentration points, making the weld extra vulnerable to splitting and failing under tons. The existence of porosity likewise deteriorates the weld's resistance to deterioration, as the caught air or gases within deep spaces can react with the surrounding atmosphere, bring about deterioration with time. In addition, porosity can prevent the weld's ability to withstand stress or effect, more threatening the total top quality and dependability of the welded framework. In essential applications such as aerospace, auto, or architectural buildings, where security and sturdiness are critical, the damaging impacts of porosity on weld quality can have serious consequences, stressing the relevance of lessening porosity with proper welding methods and procedures.
Methods to Decrease Porosity
Furthermore, making use of the appropriate welding criteria, such as the correct voltage, existing, and take a trip speed, is vital in preventing porosity. Preserving a constant arc size and angle throughout welding additionally aids reduce the probability of porosity.

Making use of the suitable welding technique, such as back-stepping or using a weaving activity, can also assist distribute warmth uniformly and lower the possibilities of porosity formation. By implementing these methods, welders can properly minimize porosity and generate top notch welded joints.

Advanced Solutions for Porosity Control
Implementing sophisticated innovations and innovative approaches plays a critical function in achieving remarkable control over porosity in welding processes. One innovative option is the usage of advanced gas combinations. Shielding gases like helium or a blend of argon and hydrogen can aid decrease porosity by giving much better arc security and enhanced gas insurance coverage. In addition, employing sophisticated he has a good point welding techniques such as pulsed MIG welding or changed atmosphere welding can additionally assist minimize porosity issues.
An additional advanced service includes making use of innovative welding tools. For instance, utilizing devices with integrated attributes like waveform control and innovative power resources can enhance weld quality and decrease porosity threats. Moreover, the application of automated welding systems with exact control over criteria can dramatically decrease porosity issues.
In addition, including innovative tracking and assessment innovations such as real-time X-ray imaging or automated ultrasonic testing can aid in spotting porosity early in the welding process, enabling prompt rehabilitative actions. In general, integrating these innovative remedies can considerably enhance porosity control and boost the general high quality of bonded elements.
Final Thought
In verdict, comprehending the science Your Domain Name behind porosity click to investigate in welding is crucial for welders and producers to generate top notch welds - What is Porosity. Advanced solutions for porosity control can even more improve the welding procedure and guarantee a solid and reputable weld.